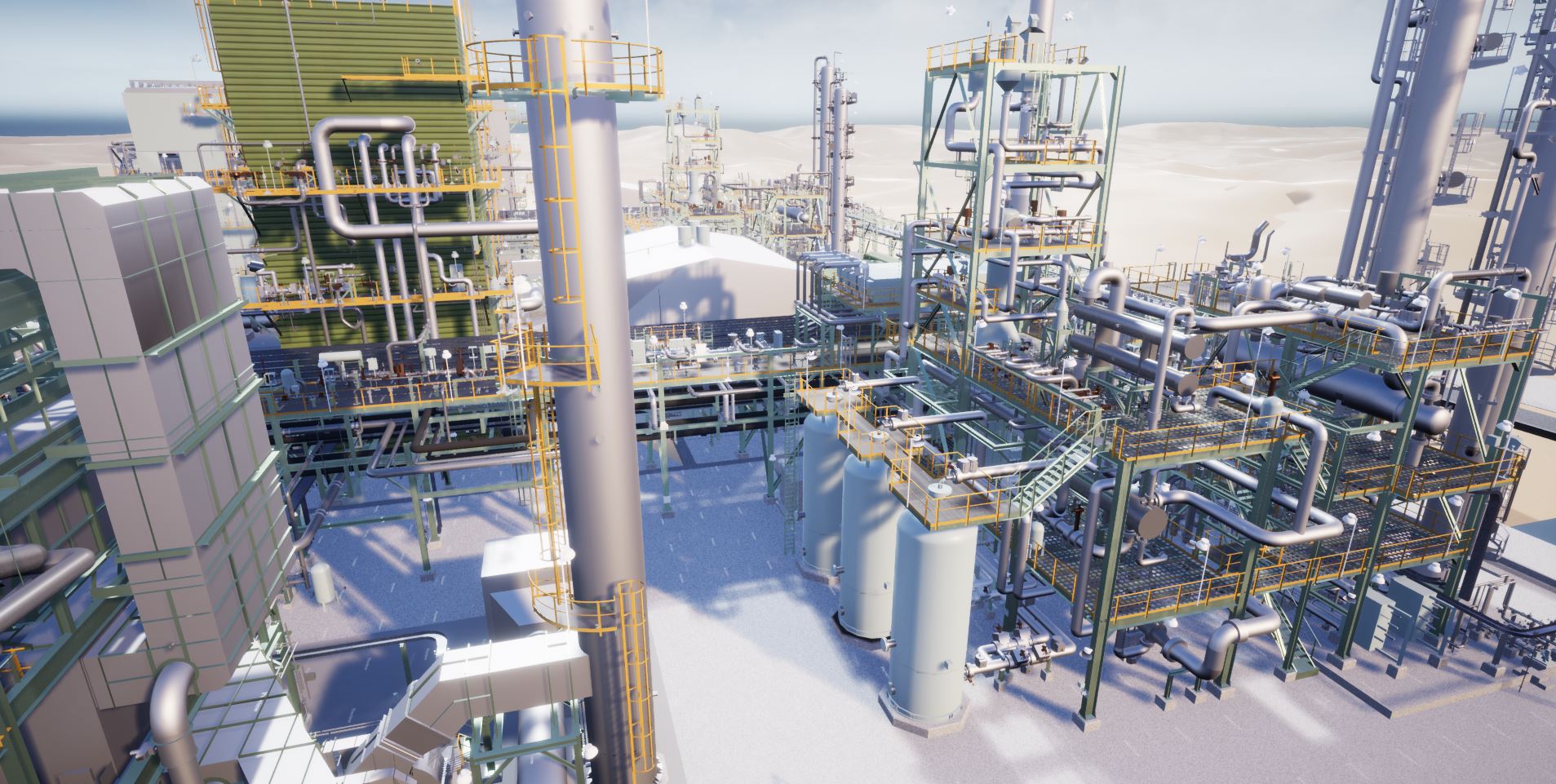
October 15, 2021
Why is it important to recreate lessons learned in industrial plants?
An industrial plant is a challenging place to work. Although these facilities are carefully designed, incidents still occur from time to time. Everyone’s aim is to prevent accidents, but are plants doing enough? Keep on reading to find out.
Knowledge keeps getting lost.
Even though industrial plants are incredibly well engineered, the whole precision invested in building one doesn’t prevent an accident from happening because of an important factor: human error. Whether we’re talking about fires, explosions, gas leaks, hazards at height or anything else, it is clear that they all result in a significant loss of production for the industrial plant, and most importantly, there are potentially fatal risks for the plant operators. Dangerous incidents must be avoided, and the best way to do that is by ensuring that all plant personnel learn from previous mistakes.
Often when an incident happens, plant personnel live through the consequences and learn from their mistakes and the mistakes of others, and in this way, they get practical experience and the plant operators can improve the working procedures based on the lessons learned.
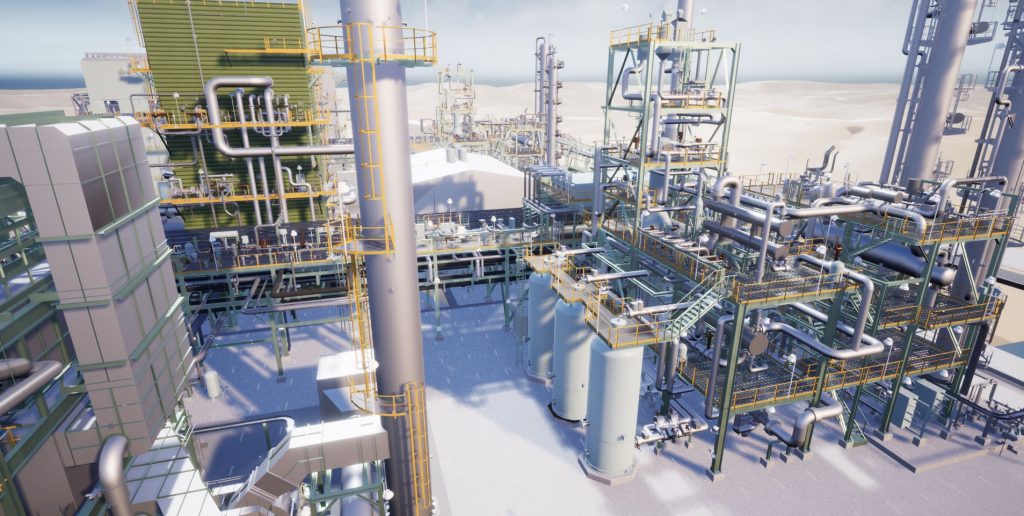
However, over the years, experienced operators who lived through various events retire, and new recruits have to learn the same lessons by reading about what happened to their predecessors and through manuals and procedural documents. This type of theoretical learning is highly ineffective because it relies entirely on the readers’ imagination and their ability to learn from endless stacks of documents. The inefficiencies of reading and other classical methods of learning were described in one of our previous blogs. Check it out to see if you should consider the alternatives and join the digital transformation.
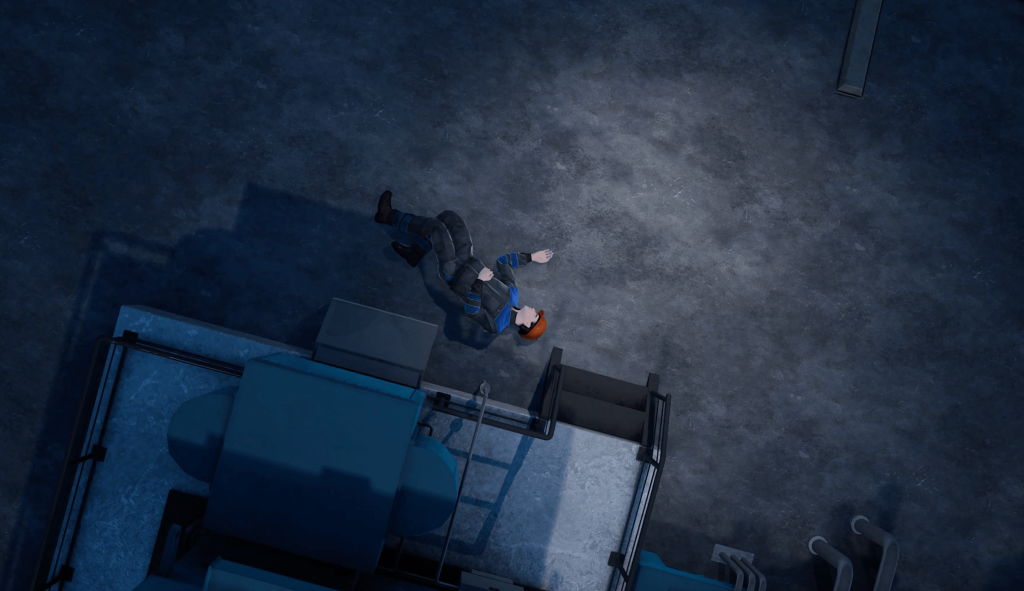
So why is Virtual Reality a better way to train plant operators?
Bearing in mind the inadequacies of the old-school learning methods and the workforce turnover, a learning revolution had to happen in the oil and gas industry. It arrived in the form of virtual reality (VR), which allows us to simulate any incident that operators experienced in real life but in a virtual world. Although they are in a safe and controlled environment, when new recruits put a VR headset and gloves on, they are instantly immersed in a life-like scenario that accurately resembles a situation experienced by their predecessors.
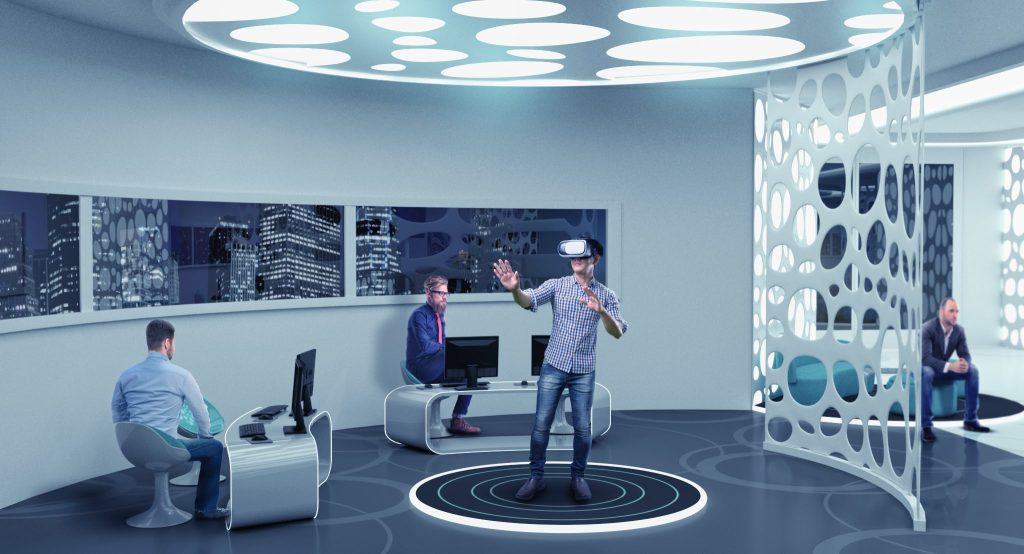
Because VR is so engaging for users, recruits quickly learn the correct protocols for responding to various incidents and retain the information much more effectively. In fact, studies show that VR teaching methods result in 4 times more knowledge being retained, compared to theoretical learning and job-shadowing. In addition, trainees gain greater confidence, have greater focus while learning and while implementing procedures in the field, and learn significantly faster. The specific numbers and all the benefits of VR learning can be found here.
One of the main issues in the gas industry is that 70% of operators are expected to retire within the next 5 to 7 years. This shocking statistic means that soon all of their experience will no longer be shared with new staff. VR solves this problem since all lessons learned in a plant will also stay within the company forever. The library of virtual training sessions can be used by anyone at any time, which not only eliminates the issue of senior operators retiring, but also ensures that new plant operators get the same effective operational training, regardless of who their teacher is. “With Linde Virtual Academy, an operation trainee in the United States can access a scenario that happened in China 10 years ago. Their training is not restricted to a specific time or location. Moreover, new incidents that occur anywhere in the world can be recreated and added as training scenarios,” explained Feras Alhothali, a co-founder of Linde Virtual Academy.
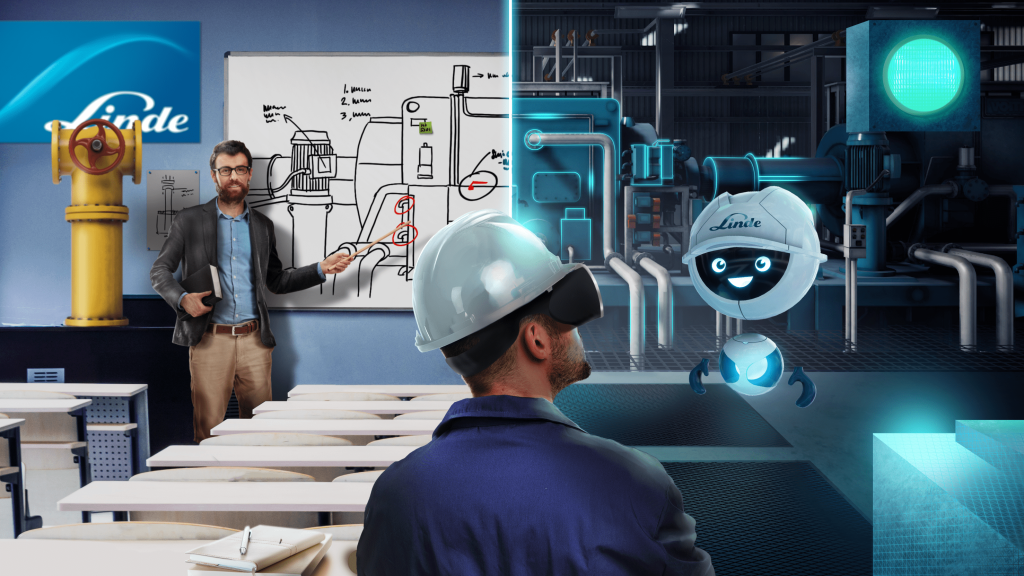
The training of the future
Linde Virtual Academy (LVA) enables industrial plants to accurately recreate as virtual simulations all the lessons previously learned by their field operators. LVA also ensures that knowledge transfer is effective, as operational training is no longer reliant on senior operators or plant shutdowns. Even the lessons documented in physical form can be recreated as training scenarios, right down to the smallest detail. Thanks to our team and Linde’s engineering know-how, we have created the best virtual reality training program for plant operators, and we look forward to implementing more technological advances in virtual reality as they are developed, thus making our platform even better. This is where the digital transformation of operator training begins. Discover more here.